Hi Brandon,
See below for responses to your followup questions:
What are considered calibrated coordinates on the system deck?
I would need to know the variety of your specific STAR-line instrument and it’s configuration to be able to follow up with specifics, but the short and practical answer is that as long as your iSWAP/instrument has been maintained on annual intervals - and any significant collisions have been followed up by a service visit - that anywhere the iSWAP can reach via VENUS commands is within calibrated workspace. Calibration offsets do not change when deck coordinates change from positive to negative relative to deck origin. As far as the iSWAP is concerned, this change is completely arbitrary.
Would defining the transport sequence as H12 rather than A1 to result in the reference the iSwap uses to place the plate in a positive X-Pos potentially change anything?
No, as long as you ensure that after teaching with last (H12) does not result in a non-zero labware angle this this will not have any impact at run time. This will have no bearing on how the iSWAP will approach a target location as it will use the center of the labware as it’s target X and Y.
What is the correct use of To Carrier and Complex movements for transporting labware off and on deck?
For deck to deck iSWAP transports (within access range of the channels) then default (“to-carrier”) iSWAP transport mode is fine in almost all circumstances. This will allow VENUS to automatically decide how the iSWAP articulates to a get plate or place plate position without the programmer having to specify. This will not have any bearing on accuracy vs complex movement. Issues with transport would be more likely due to any inaccuracies with labware definitions and taught deck coordinates
Complex movement is generally only needed to be specified in two instances:
iSWAP full extension to LHS or RHS:
When needing to use an iSWAP grip direction that forces a full extension to left or right (off deck integration or locator positions), you can use a complex movement to force full extension by using a retract distance greater than 139.0mm. This is almost never needed for on-deck to on-deck movements.
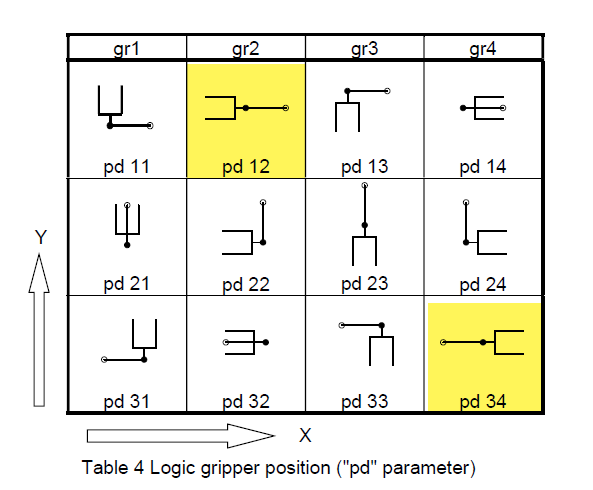
Hotel-style movements:
The general intention of complex iSWAP movements are for plate placements to/from a “plate hotel” or random access plate carrier
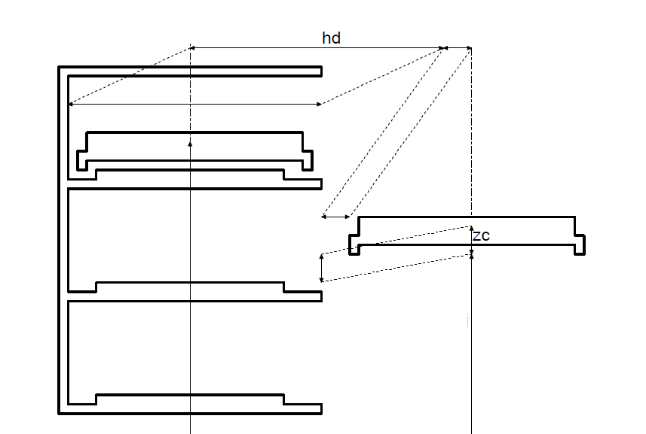
A hotel movement will use both a retract distance and a liftup height. When both of these parameters are used, the iSWAP with articulate to the required approach rotation/grip direction using a ‘buffer distance’ defined by the retract distance (will rotate prior to this X/Y coordinate so it doesn’t collide with the integration). It will then lower from traverse height to the ‘liftup height’ and then move in X/Y per the distance specified by the retract distance (because 139.0mm is greater than the iSWAP can reach with a wrist bend, this will force a full extension - if specified). At this point the iSWAP will lower in Z by the specified liftup height and release the plate, exiting in reverse order.
This effectually prevents from the hand of the iSWAP from moving to labware Z to/from traverse height prior to moving out of the way of an obstacle (plate hotel) in X/Y before moving in Z.
Neither of the above movement modes will impact iSWAP movement accuraccy,
When using a To Carrier Movement does the system try to snap the labware to the carrier?
Snapping a labware to a carrier/template site on a deck layout serves two functions, and neither are intrinsically related to how the iSWAP interacts with a labware/location at runtime - nor does it have any influence on to-carrier vs complex movement. When you snap a labware to a carrier site, this establishes a relationship in sample tracking between the parent (carrier and its sites) and the child (plate). Additionally, this will provide a convenient default starting point for the deck coordinates of the plate, relative to the carrier site.
Once a labware is snapped to a carrier location, you can then adjust the deck coordinates from default while maintaining the ‘snap’ (sample tracking relationship). For iSWAP steps, the deck coordinates of the labware are all that matter in terms of the final target location of the iSWAP. Default vs complex movement simply alters it’s approach to said target location.
Place plate on deck carrier (Complex movement) [Using to carrier movements results in the plate being placed enough distance off in the X that it crashes]
I need more details to provide further consult. A video is ideal, supplemented with a test method if it can be provided. This is required (or atleast run and communication traces) for further remote support. If it would be easier to be put in contact with your local support team, then just let me know!
It is important the the source labware used to teach off-deck labware is taught properly before using the iSWAP to teach and off deck position. If the labware definition and deck coordinates of the source/deck labware are incorrect, then you are trying to hit a moving target.
Thanks.
-Nick